据法新社引述英国克拉克森日前公布全球造船业的最新统计数字,中国造船业近年发展迅速,去年接获船舶订单达700万修正吨,以单一国家计算已成功超越日本,晋身全球第二大造船国。
伴随着中国造船量不断上扬的红线,数字背后的隐忧也逐渐暴露出来。从2005年2月到2005年4月,我国连续发生 了4起新船舶船体断裂的质量安全事故。一位造船工人谈起曾经在船厂打工的经历更是心有余悸:“我在某地个体船厂打工的头两个月吓得睡不着觉,那简直就是人有多大胆,就造多大船,据说那个船厂还是那一片比较好的。”
有行业人士说:“中国造船千万不能忽视‘短板痛’,只有实现量和质的同步跨越才能成就中国迈入世界造船第一大国的最重砝码。”
近日,长江船舶设计院副院长徐伟在接受记者采访时更是一针见血指出:“中国造船的‘世界第二’称号决不能成为‘垃圾造船’的代名词。”他认为,杜绝劣质船要从管理系统上抓,其中规范设计资质是重要的步骤。此外,造船技术含量、信息化应用等正越来越受到人们的普遍关注,只有加大科研投入、增强造船的高技术附加值,中国造船业才能顺利实现加速发展的目标,要突破技术瓶颈还需要加强高端产品的针对性研发,在科研政策扶持、规范船舶设计和船舶检验市场等方面加大投入。
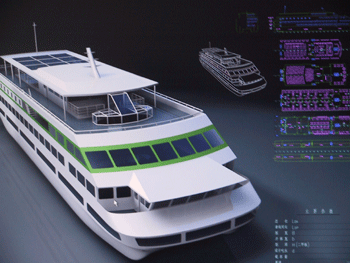
“刀把子”要握在自己手里
早在19世纪,恩格斯在《反杜林论》中就指出:“现代的舰船不仅是现代化工业的产物,而且同时还是现代大工业的缩影,是浮在水上的工厂。”100多年来,随着造船技术不断发展,特别是近年来以自动化为代表的高新技术以及各种新工艺、新材料的广泛使用,造船技术在集成和高技术基础上不断创新,现代船舶工业已发展成为高技术支撑下的现代产业。
设计是现代船舶工业发展的前提和关键环节。中国船舶工业经济研究中心联合上海船舶工艺研究所的有关专家曾表示,采用FMI要素体系对我国造船技术水平进行了评估。结果显示,目前国内9家大型船厂的平均总体技术水平值为3.3,比1998年时的3.09上升0.21,与国外先进水平的差距大致为14年左右,比1998年时的15年缩短了1年。
为什么中国造船业“赚钱难”?很重要的一点,难在设计关。据悉,中国船舶工业总公司去年交付了约100万净吨位的新船,金额约为6亿美元,其中80%的客户为外国公司,但其利润仅为570万美元。官方数字显示,整个中国造船业去年的总利润是3600万美元。在巨额的新船完工量和相对微薄的造船利润落差中,设计费用的流失是很大一个原因。“造船的‘刀把子’还控制在别人手中”,有行业人士如此说。据了解,我国造船业传统方式是“先合同后设计,边设计边建造”,普遍存在设计周期长,设计深度不够,设计软件依赖国外引进、造船核心技术知识版权归属国外造船强国的问题。在中国造出的船舶中,属于国内自主开发的产品不多,很多船舶的原始设计来自国外,特别在高新技术船舶方面,仍然没有摆脱主要依赖船东或国外设计公司的被动局面。
业内专家认为,中国船舶工业与日、韩、德等先进造船国相比仍有很大的差距,首要表现在船舶设计和建造技术落后,技术装备水平、产品开发能力均明显低于先进造船国,出口船舶的船用自动化设备基本依赖进口。业内人士告诫,中国要想彻底改变“只赚吆喝不赚钱”的局面,从造船总量中提升经济效益,当务之急是须突破船舶“设计之门”。
船型开发能力薄弱,已经成为影响中国造船业进一步发展的重要因素。日本、韩国船厂在船型开发方面做得很好,现代重工、三星重工等每年向市场推出20多种标准船型,引导着市场走向,掌握着竞争主动权。而我们由于缺乏品牌产品,只能是经营跟着市场跑,设计跟着订单走,十分被动。
不过,种种迹象表明,国内造船业正越来越重视自主创新和造船品牌的塑造。“中国造”锋芒已直逼日本、韩国。据业内人士介绍,建造散货船原本是日本造船企业的优势,过去,欧洲船东在订购散货船时较多地选择日本船厂。然而,近年来中国造船“异军突起”,中国最大的现代化船厂上海外高桥造船厂,目前已成为世界好望角型散货船建造中心之一。 除了散货船以外,中国造船企业近年来在集装箱船、油船等目前世界主流运输船建造上也在不断突破。浮式生产储油船、液化石油气船、液化天然气船建造的专业技术水平不断提高。此外,紧跟国际市场需求,近年来,中国造船企业建造的集装箱船也不断大型化。
从建造17.5万吨好望角型散货船,到打造中国首艘30万吨级巨型油轮,中国造船业实现了巨型油轮“国轮国造”零的突破。翻开近年来中国造船记录,迈过一个个“空白点”的步伐清晰可见。
国内船舶设计机构也正在一改以前设计上的被动局面,不再只满足于“来料加工”,而是开始了超前开发,并有一定的技术储备,从被动的按照船东要求来设计,到主动地去收集、分析各种船东的需求,主动与船东联合开发,向市场推出具有自主知识产权的产品,技术上的主动性大大提高。在这样一种意识的指导下,长江船舶设计院近年来船舶设计自主创新品牌层出不穷,技术核心竞争能力进一步增强。设计的产品有的填补了国内空白,有的达到或超过国内先进水平,其中部分成果荣获了国家科技进步一等奖和国家科技进步二等奖。如:由长江船舶设计院设计的平底船——江海联运疏运模式(ATB)船组即“ATB敞口集装箱船队”,在中国最大的集装箱港——洋山港正式交船,从而奠定了该院在ATB船队建造设计领域的领先地位。除此之外,该院在江海直达船、海上工程船、海上桥梁工程船、浮式自卸码头项目上的设计上也新的突破,他们研发的LPG船已形成系列化、不同档次的船型设计深受市场欢迎。“下一步,我们还将在油轮、大型集装箱船、工程船、化学品船等船型设计方面进行技术攻关”,徐伟建议,要提高国内造船业的技术设计水平,设计企业可以通过联合设计来学习国外造船先进技术,再自主创新取得知识产权。
船舶设计专家顾建国高级工程师如此评论:“设计是造船之母。国际船舶市场竞争的焦点就是产品创新能力的竞争,只有拥有自主开发能力,拥有品牌产品,才能赢得竞争,扩大市场份额”。
瓶颈突破尚需时日
一位行内人士透露,国内大型企业,如中海集团、中远集团的集装箱轮、散货轮等普通船舶,眼下基本都用国产船,但豪华的游轮则几乎都依靠进口。中海集团现役的4条游轮清一色就是从荷兰进口而来。事实上,豪华游轮等高档船舶,由于技术含量大、附加值高,已经成为造船业的“肥肉”,而传统的油轮、集装箱船和散货船等由于市场竞争激烈,利润趋薄。韩国等造船发达国家已经开始逐渐实现生产重心转移,啃骨头的同时,纷纷盯住了高端市场的肥肉,各大造船厂开始转向技术含量较高的高附加值的造船业务。
据了解,实际上在80年代中的时候,韩国造船和中国造船水平并没有很大的差距,发展到今天,中国造船水平和韩国造船水平的差距其实主要还是体现在企业的管理和造船新技术的研发上面,包括新船型的开发和真正建造技术、设计技术的研究。据统计,大宇船厂和三星船厂从事设计和建造技术的人员要超过一千人,但在国内某大型造船厂,真正从事设计的人员才280多人。日本、韩国以及欧洲一些国家的造船厂已经集中力量发展技术优势,基本实现了由模块化向数字化模式的转变。而目前中国造船业竞争力主要集中于劳动力成本优势,我国船厂的工人费用仅为日本的1/20,是韩国的1/10,大多数船厂尚未完全达到模块化造船,企业规模偏小、科技创新能力尚且不足。
业内人士认为,只有在船舶产品设计开发中融进设计的精细,融入设计成本的降低,甚至通过造船技术的研究来提高造船企业的生产效率,造船企业的发展才会有所促进,企业才会有生命力。
“中国造船业的战略升级已势在必行,这种升级不能仅仅是低水平扩张的加大投入——投了,软件跟不上来不行,软件和硬件必须要匹配,软硬兼施才能达到效果。”
长期以来,因体制所限,我国的企业与科研机构之间存在着“两张皮”现象,科研院所的人才与技术优势由于缺乏合作对象得不到发挥,手握订单的企业却要舍近求远,高价聘请国外的设计机构为其承担设计任务,这种状况严重地束缚了民族工业的自主创新能力。韩国高端船舶产品研发渐入佳境的原因之一就在于国家重视造船、汽车等民用型工业的壮大,从而带动了有关企业对这些产品研究投入力度的加大。有专家建议,国家要对船舶研发机构进行“扶优汰劣”,甚至应在一定程度上向这一领域进行政策上的倾斜。
徐伟说“韩国船企每年产值的3%都用于高端产品的研发,这一点足以让国内造船船舶设计机构羡慕不已。”他建议,国家有关主管部门还可以设立设计资质管理机制,建立扶持基金,在税收、批地和经费投入上扶持有能力有技术储备的此类民用型产品研发机构,这样一来才能大大拓展高端船舶产品的研发空间。
设计市场需加强规范
低质量船舶,指无审批图纸,或未按图施工,或造船工艺达不到船检法规和规范要求,或建造质量低劣,或未完成必须的建造检验项目而生产出来的船舶。 低质量船舶一部分缘于违规建造,即所谓的“滩涂造船”。“租一块滩涂,买一堆废旧钢材,雇一群民工,经过半年敲敲打打,一艘几千吨的船舶便下水了”,这是对我国一些地区违规建造船舶的形象说法。这类船舶大部分无图纸,强度和稳性一般都未经计算,船舶焊接质量差、内应力大,选择构件尺寸小、强度不满足要求,主甲板和船底板厚度不够,大量使用非船用钢板等。一些船还使用旧设备,存在低配置现象。在正常风浪中也容易出事故,小的海损容易产生大的沉船事故。油船、化学品船、客船出现事故后社会影响大,其后果非常严重。特别是重大污染造成生态环境破坏是不可估量的。
“低质量船舶的另一成因不可忽视,那就是造船设计方面的薄弱”,徐伟对此有另外一种认识。“现在我国的造船设计市场规范力度还不够,相对比较混乱,没有设计师的资质考核认可机制,一个大学毕业生往往毕业后只要进入设计公司就可以开始搞船舶设计了,这样设计出来的技术性能如何保证?不可能形成国产自主知识产权的核心技术。”徐伟对此不无忧虑。
有人士认为,中国的造船设施,就规模和先进性而言与发达国家比相差10年或更大些。中国造船工业生产效率大大低于发达国家,有资料表明,中国船舶工业生产效率约为发达国家的1/7-1/10,这里很可能还未考虑员工数量的差别,若按人均产值或人均产量对比,中国船厂的生产效率可能为发达国家的1/20或更低些。此外,从中国造船技术的现状和先进国家的差距来说,中国通用船舶(散货船、油船等)设计技术接近国际水平,但同型船钢材用量偏高,经济指标偏低,生产设计的深化程度约为发达国家的50%~60%,设计差错率则远远高于发达国家。
一位曾在江南造船厂工作过的员工举了一个形象的例子:同样造大型船只,在日本等技术高度发达的造船企业中,由于精密度高、设计能力强,在造船过程中能化整为零,将一艘大船分拆成数块,各自完成各部委的水管铺排等生产步骤,在各块都制造完成后,拼接组装在一起就可以了。而国内的造船企业,绝大多数还是从基本的打造船体的整体、逐步铺设管道、安装甲板等传统的生产步骤做起,在生产效率上与前者相比,差距非常大。现在国内企业在技术上已经有所进步,但也只能做一些甲板的分块生产拼接等等,像国外那种分块生产组装的技术,国内由于技术、设计精密度不够等原因,还难以做到。
有专业人士表示,“中国造船要强大,当务之急之一是加强设计人才的储备和培养,核心人才是关键,同时要加强设计市场的规范化管理和运作”。
市场竞争的激烈,使得世界各主要造船国家为求得领先地位,纷纷加紧进行船舶企业技术改造和企业结构调整,获得了快速发展,而中国的造船业,能否迅速缩小与韩、日的差距,如何调整是一个关键,也许中国造船的首要之务就是要掀起一场“头脑风暴”。